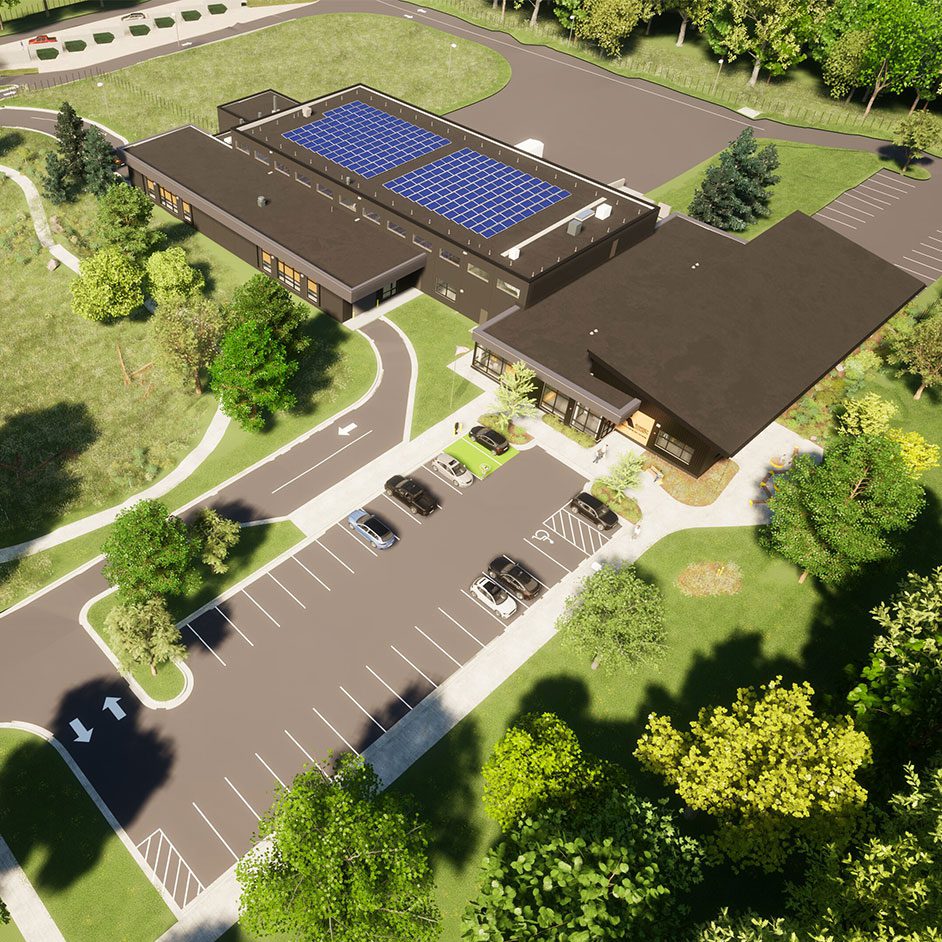
Thrifty humans have been reusing and recycling resources for millennia. But most municipal recycling programs owe their existence to the environmental movement of the 1970s.
Today, recycling centers are a fixture in many American communities. They divert metals, plastics, paper, organic matter, and hazardous waste from landfills. In some cases, recyclables are even resold, generating some measure of revenue for cities and counties. This is the circular economy at its best.
In recent years, driven by a desire to reduce carbon footprints, many communities have elected to invest in new or upgraded recycling centers. LHB has tracked this trend. In 2021, Ramsey County retained us to design its new 35,667 SF environmental service center, which aims to be a model facility, focused not only on recycling, but also on reuse and repair. A year later, we successfully won a contract to design a new 19,125 SF recycling facility for Dakota County, currently in construction documents.
To land these projects, our government group has leveraged its experience in public services and operations facilities. But with each new recycling center design, we become more and more knowledgeable about what it means to serve this growing niche. Among the lessons we have learned:
Volume is increasing
As public interest in recycling grows and markets for recycled materials expand, municipalities anticipate their facilities will have to handle larger loads. Sorting areas must be flexible enough to handle increased volumes and changing workflows. Dakota County’s recycling program encompasses appliances, scrap steel, scrap aluminum, bulky waste, organic tires, and textiles, with possible expansions for carpet recycling and paper shredding. The county also plans to extract rare metals (such as lithium) from electronics waste.
Customer experience and education are a priority
The new recycling centers are more than just drop-off and sorting facilities. They also contain classrooms for environmental education and workshops where residents can access tools to repair small appliances and gadgets. Ramsey County hopes to develop classroom programming around recycling, reuse, repair, and hazardous waste. For example, rather than landfilling a broken toaster, residents might attend a workshop where they learn how to fix non-functioning items.
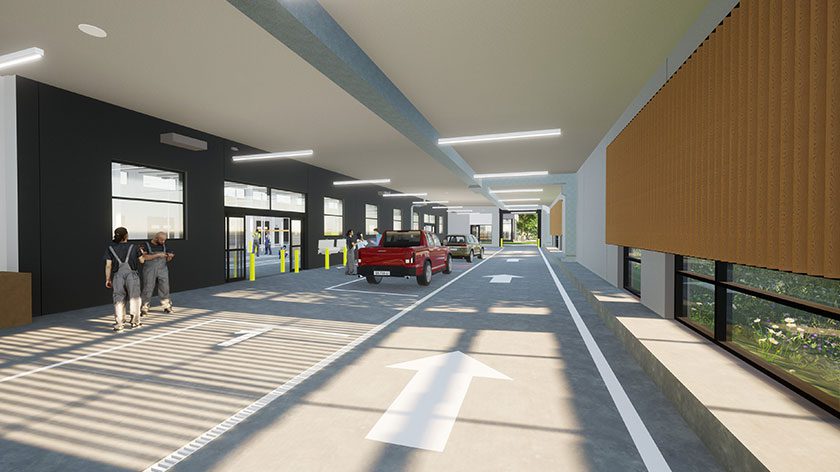
Circulation is complex
Increasingly, designers of recycling facilities must consider the circulation of multiple groups. Residents arriving in passenger vehicles for a class don’t want to tangle with semis unloading aluminum cans. Loading docks need to be large enough to accommodate multiple kinds of workflows, and site planning must allow for the safe movement of semi-tractor trailers, roll-off trucks, forklifts, skidsteers, and wheel loaders. Plus, the secure storage of flammables and hazardous materials must be considered.
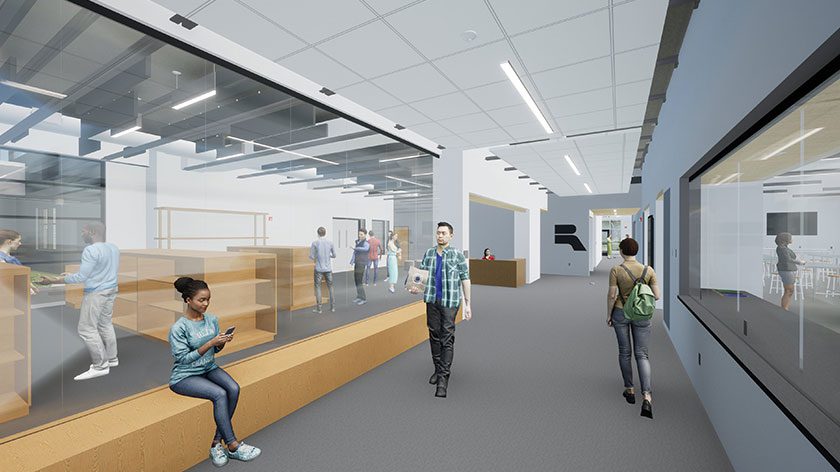
Training is also a goal
As the recycling industry grows, jobs associated with the activity are also expanding. LHB is currently designing the Goodwill Training and Resource Center on the former U.S. Steel site in Duluth. This project, a new 109,500 SF building, is focused on workforce development and workforce reentry, including programs for formerly incarcerated individuals. Participants are taught how to extract springs from old mattresses so the metal can be sold as scrap. It’s another example of how recycling and the circular economy go hand in hand. ∎
Contact LHB Architect Aaron Kelly to learn more about trends in recycling center design.